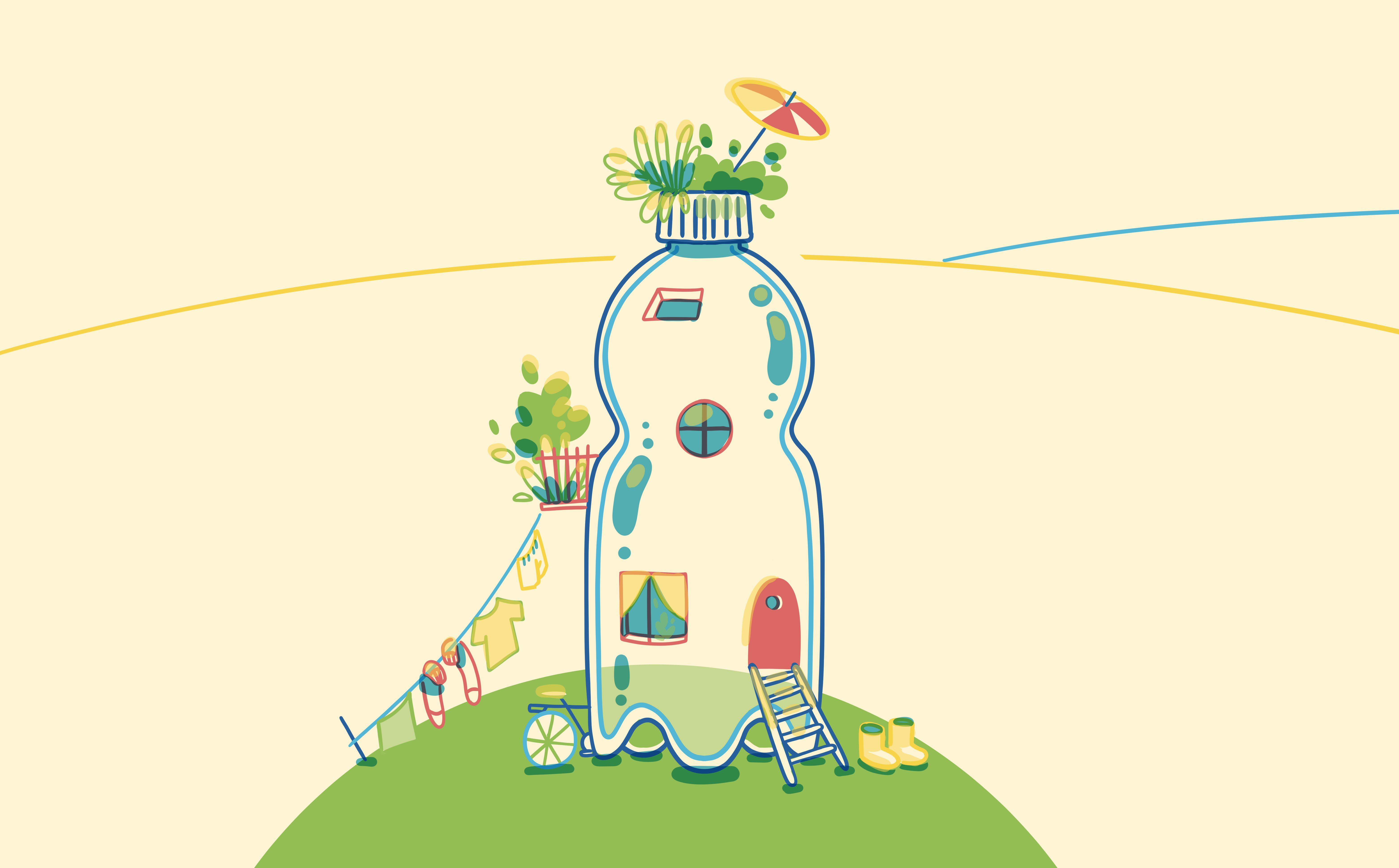
Is plastic waste the building material of the future?
- Written by Désiree Schneider
- Illustration by Frauke Berger
Using recycled plastics as a building material is already normal in other regions of the world and can solve two problems at once. A text for those who have had enough of concrete.
The plastic bottle disappears into the mud. David Heitmann carefully covers it with the clay mixture. He reaches for the next bottle and bricks it in, next to it the next and the next. Slowly, the wall takes shape.
More than a hundred 1.5-liter bottles have already found a place there. Each bottle is filled to the brim with half a kilo of plastic waste that would otherwise have been incinerated or ended up in the environment. Instead, it finds a second life as building material here in the “recycling village” on the edge of the rainforest on Sumatra.
The recycling village is a collection of buildings in the tourist village of Bukit Lawang in Indonesia and was created by a young environmental protection organization from Koblenz, Germany called Project Wings. Since 2019, the non-governmental organization has built seven buildings from local plastic waste together with the locals and their civil engineer David Heitman. Among them are a school, a building with sanitary facilities and a co-working space. For all of this together, the islanders and Project Wings collected more than 50 tons of plastic waste, cleaned it up and processed it into more than 100,000 “Ecobricks”, i.e., PET bottles filled with plastic waste.
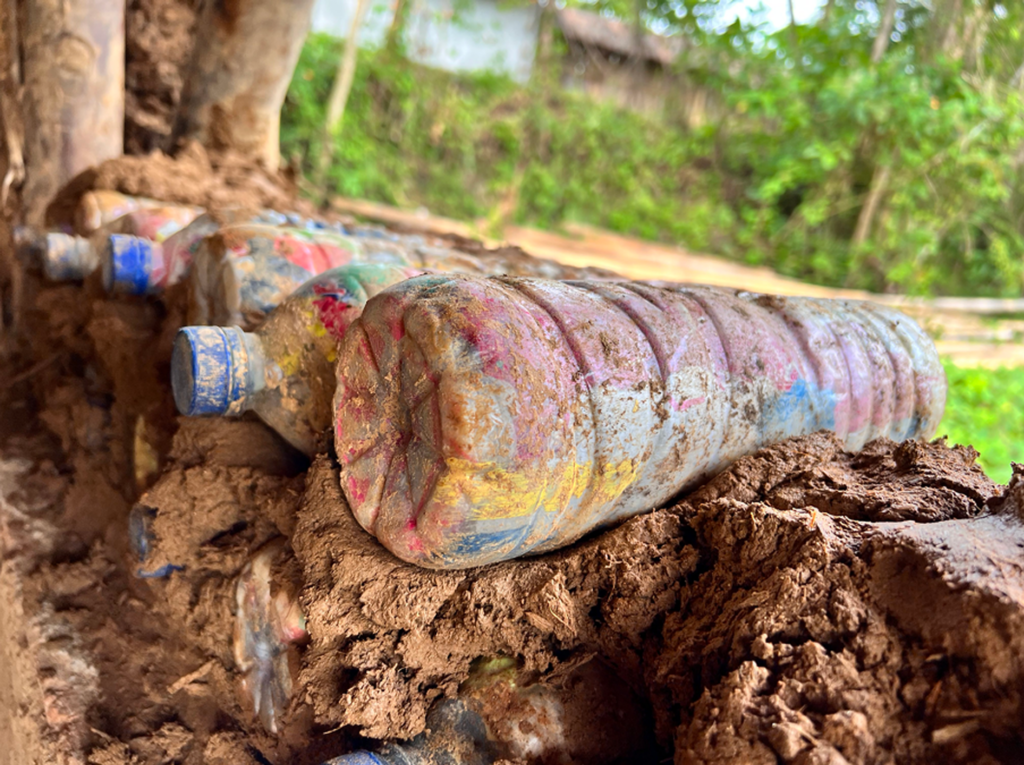
Content for the Ecobricks is easy to find on Sumatra and the neighboring islands. Plastic waste is an almost endless resource – and not only in Indonesia. Only 9% of all plastics produced since the start of industrial plastic production in the 1950s and accumulated as waste have been recycled to date. That is the estimate of the Organization for Economic Cooperation and Development (OECD).
Anyone who travels just a few meters off the beaten track in Indonesia can see and smell the problem.
Plastic waste piles up in open landfills by the roadside. From there, the wind blows it into nature and nearby bodies of water – or it ends up there in the first place. The plastic clogs riverbeds and contaminates groundwater. People also bury it on beaches or in forests to get rid of it.
Around 71% of all plastic ever generated has been dumped in legal and illegal landfills or directly into the environment, according to the OECD.
Because plastics do not biodegrade, they break down into microscopic particles in land and water. In the process, they release toxic substances and cause great damage worldwide. About 80% of the plastic waste in the world’s oceans comes from land.
Plastic waste is often openly burned in Indonesia (as in many other countries). There are hardly any safety precautions. Residents are exposed to toxic fumes that can cause respiratory problems, cancer and birth defects. The OCED estimates that 19% of the plastic waste ever generated was incinerated, usually legally, for energy generation.
The industrialized nations of the Global North – the USA, Germany, Great Britain and many more – are to blame for the precarious waste situation of many countries in the Global South. They have used countries like Indonesia as dumping grounds for decades, regardless of the consequences. Although more and more affected countries are imposing bans on garbage imports, Germany and others continue to look for buyers who will buy the unloved plastic, which cannot be recycled, from them for little money. Drowned in foreign waste, the governments concerned are finding it difficult to establish functioning waste systems and deal with the pollution.
More and more companies and organizations from industrialized nations like Project Wings, but also from the affected countries themselves, want to help by collecting the dirty plastic waste from nature and giving it a new life: as building material. This is intended to solve a second global dilemma at the same time: the construction industry's growing hunger for raw materials.
It is one of the industries with the highest consumption of resources and the largest volume of waste. The production of concrete, the most widely used building material in the world, accounts for 8% of annual global CO2 emissions alone – and demand is rising.
That’s because 96,000 new affordable homes would need to be completed every day to accommodate the three billion people estimated to need homes by 2030, mostly in Africa, Asia, Latin America and the Caribbean. That’s according to calculations by UN-Habitat, the United Nations’ human settlements program. Resources are running out.
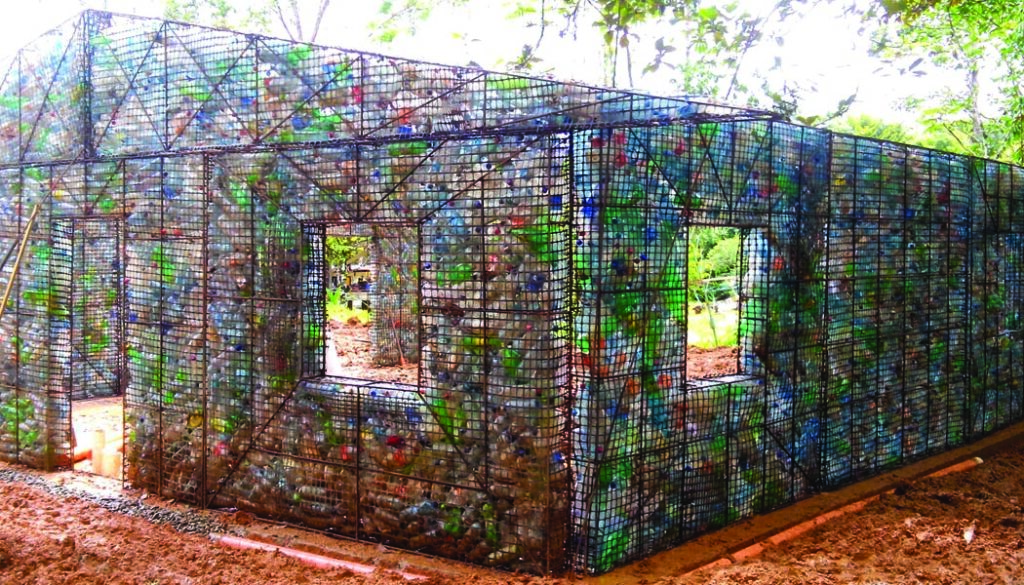
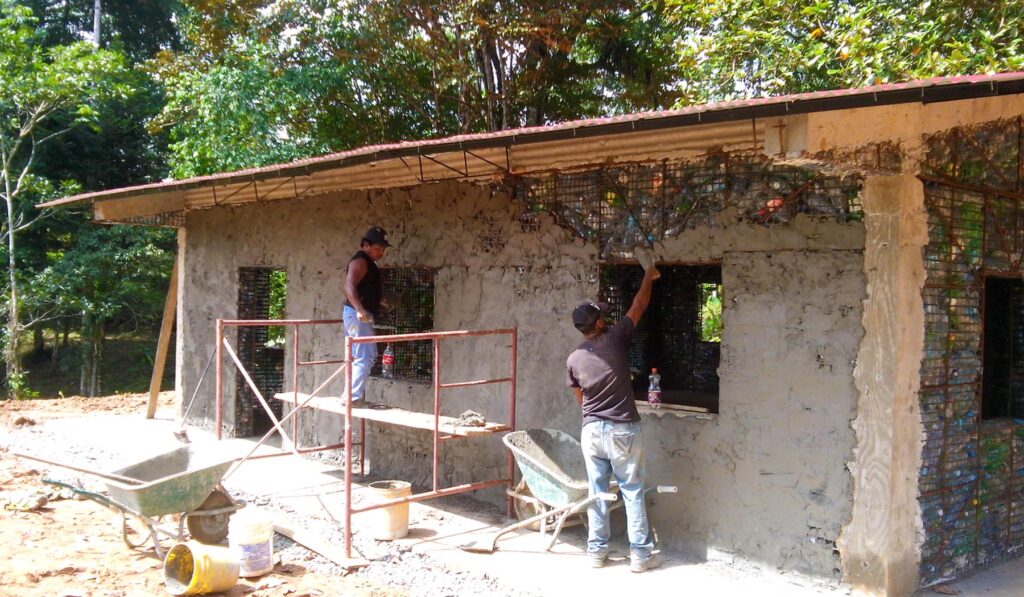
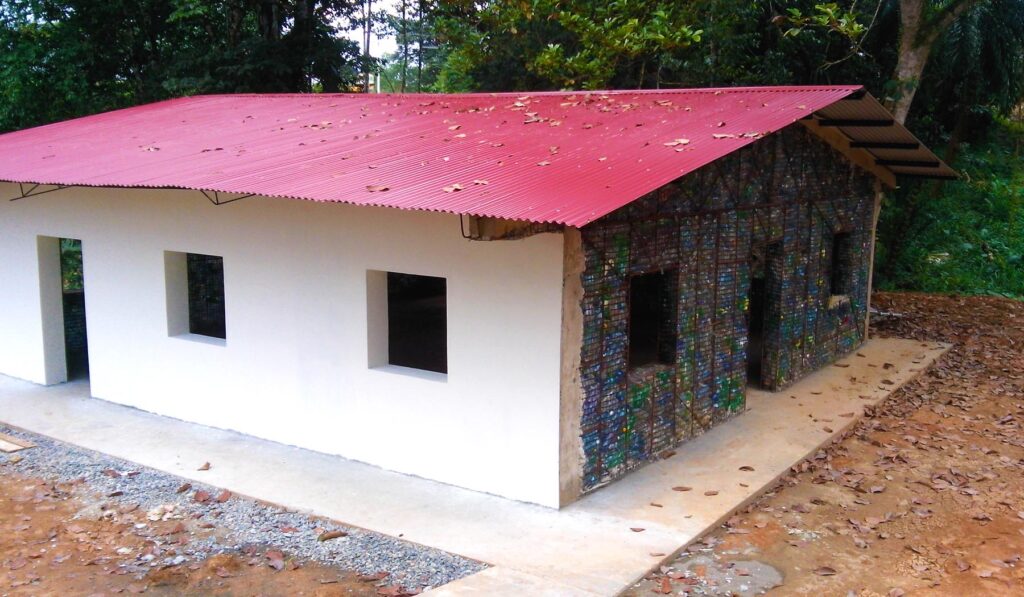
Are plastics suitable for building?
Window frames, garden fences, pipes, vinyl flooring, silencers, seals, benches – many components of a house are made of plastics. The fact that this is so commonplace today is due to the practical qualities of the material: depending on the type, plastic can be flexible and malleable, but also very strong and water-repellent. It can be heat insulating and at the same time resistant to heat and sound. And most importantly, it is durable and inexpensive. However, the last two advantages become disadvantages as soon as plastic accumulates as unwelcome waste.
Most of the plastics that are used today were manufactured specifically for the purpose of construction. Some products contain a small amount of recycled plastic. Rarely do they consist of 100% recycled waste plastic, and even more rarely is this plastic trash that comes from nature or landfills. This is because it is particularly difficult to reprocess. Therefore, the few flower pots and park benches made from 100% recycled plastic are expensive, so far.
More and more researchers and entrepreneurs in the construction industry are now looking for new methods of processing plastic waste and returning it to the cycle - not primarily as flower pots or park benches, however, but as something more substantial with greater relevance.
From the crammed plastic bottle to the oversized Lego brick: the ideas are so different
The main purpose of a wall is to support the roof and floor of a house and provide protection from the elements. Non-load-bearing walls are used to further divide rooms within the house or apartment. To build a wall, several elements must be layered on top of each other, much like a burger.
Masonry, the load-bearing structure of the wall, is often made of concrete, clay, loam or sand-lime brick. These could be replaced on a large scale by recycled plastic waste, as studies and practical examples have shown in recent years.
Some companies are replacing traditional building materials in masonry with stuffed plastic bottles, while other companies operate a more elaborate process. They melt down the plastic waste, press it into bricks or mix it with other materials such as sand, dust, rubble, crushed glass or sawdust. This requires appropriate equipment such as melting plants or presses, and therefore also costs more. Some make their ideas and the manufacturing process openly available to others (open source), while others want to make a living from it or even profit from it.
The following are the three procedures that are currently the most widely used.
Ecobricks: walls made of plastic bottles
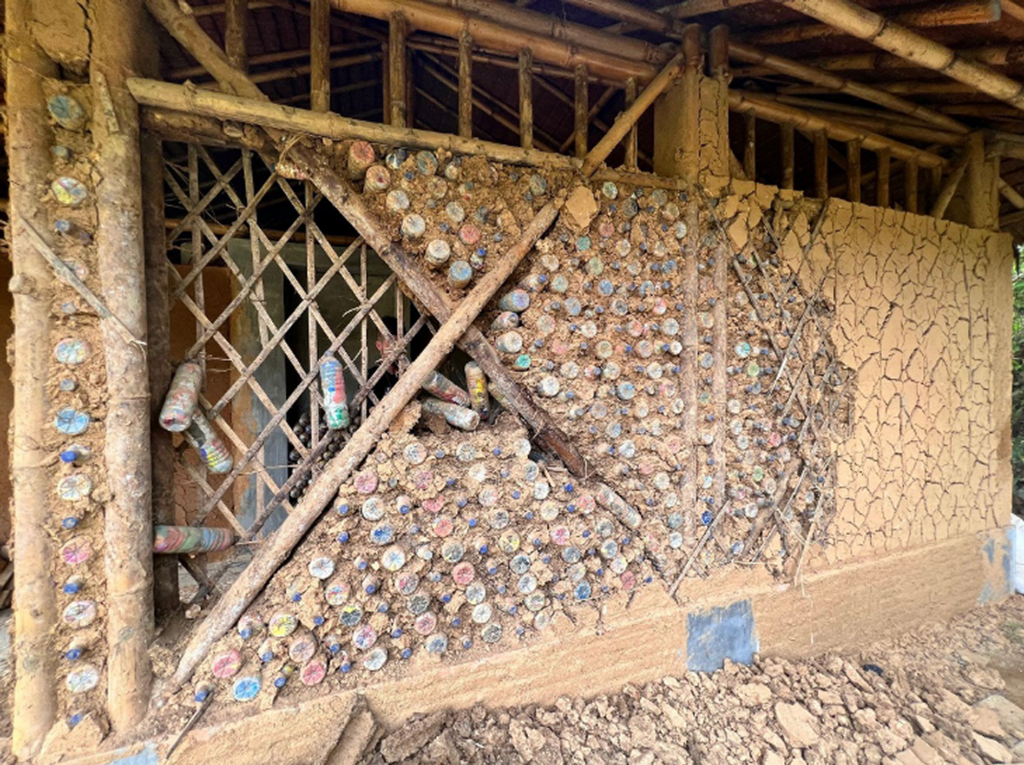
Back to the recycling village in Indonesia. There, in close cooperation with the locals, Project Wings uses what is probably the simplest, yet most widespread construction method, Ecobricks. The nonprofit organization from the Rhine region made a conscious decision to use them:
"We wanted to find a solution that was as low-threshold as possible, inexpensive and easy to implement. One that everyone can participate in and help out with. We're not just about building houses and reducing plastic pollution. We want to change people's awareness of plastic and work with them on an overall solution that can be easily copied and transferred to other regions of the world."
David Heitmann, building engineer of Project Wings
The 29-year-old volunteered to plan the houses for the recycling village. The NGO has introduced a deposit system in which more than 300 people from the region currently participate. “They can collect plastic themselves from nature and their households, make Ecobricks and hand them in to us,” says David. For each Ecobrick, the locals receive the equivalent of 42 cents, which is enough for a warm meal and represents a small additional income for many families.
Other Ecobrick buildings are already standing in Nigeria, South Africa, Guatemala, Panama and the Philippines. They are used to build single-story houses, classrooms, emergency shelters or raised beds. There is even a hostel. Playgrounds, garden decorations or benches made of Ecobricks can also be found in Great Britain. Residential buildings are not allowed to be made of them there, due to a lack of tests and regulations on construction methods.
The construction technique is open-source and available for all to see. The Global Ecobrick Alliance (GEA) lists only three specifications on its website.
First, only non-recyclable plastic waste shall be used or such waste that has previously polluted the environment.
Second, the waste plastic must first be washed, dried and then stuffed tightly into the bottles, preferably with a stick. A 0.6 liter bottle should weigh at least 200 grams and a 1.5 liter bottle 500 grams. This will make the Ecobrick load-bearing and more fire-resistant.
Third, ecobricks should be used only for small, single-story buildings. For construction with Ecobricks, the company recommends installing the bricks horizontally in clay mortar. An alternative is to reinforce the structure of the house with steel bars and wire mesh.
From the research, we know that building with Ecobricks is:
- Cheap. In a refugee camp in Bangladesh, the construction costs for emergency shelters were reduced by 54%.
- Relatively earthquake-proof because they are light.
- Easy, since no professional training is required.
- Stable. Ecobricks are up to 20 times stronger than conventional clay bricks – depending on the filling material.
- Secure. If the Ecobrick is encased, it is protected from UV rays, water and heat.
- Removable. The bricks can later be used elsewhere.
Building with Ecobricks is also:
- Labor-intensive. All bottles for a construction project must weigh about the same.
- Not standardized. There is no way to use prefabricated parts and so far no uniform construction method. Therefore, the building and planning regulations of many countries will not allow this type of construction.
- Flammable. When Ecobricks burn, the plastics release highly toxic gases.
- Not safe from microplastic abrasion if the bottles are not fully coated.
- Best suited to tropical climates. The construction does not store heat well.
Which initiatives are already working with Ecobricks? The training company Global Ecobrick Alliance is leading the network by, encouraging private individuals worldwide to produce and use Ecobricks. Additionally, mumerous NGOs such as Project Wings (the recycling village in Indonesia), Hug It Forward (Guatemala), The Circle Hostel (Philippines), Khensani’s Collection (classrooms in South Africa), Robert Bezeau (Plastic Bottle Village in Panama) are already utilizing the technology.
Bricks made from a plastic waste mixture
Probably the second most commonly used variant is to add a certain proportion of waste plastics to clay or cement bricks. This is intended to save resources and, above all, costs. The possible combinations of which type of plastic is mixed into the brick and how much of it are almost endless. Most companies replace a proportion of 5-25% of the concrete mass with plastic waste from the packaging industry. The plastic is washed, shredded, heated and added to the concrete. Some manufacturers also mix in glass dust or other additives.
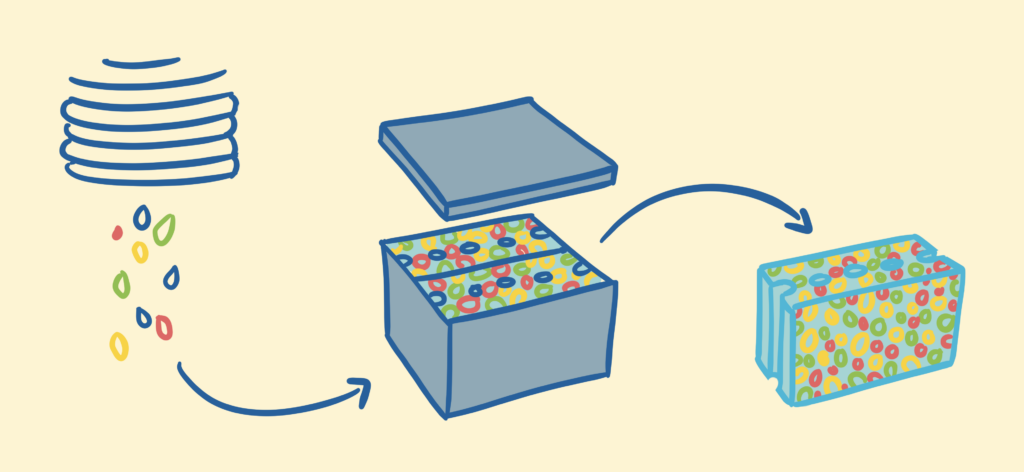
The different methods are difficult to compare: The companies do not make their exact compositions public; after all, they want to earn money with it. And there have been only a few studies on the subject so far that are meaningful. What is striking, however, is that almost all the research projects and companies on this method come from India and Africa: from places where plastic pollution is high, where there is little or no recycling infrastructure, and where there are many unemployed people. For them, it’s more than just a stopgap measure to use plastic waste against housing shortages. It’s an opportunity to create jobs and valuable housing, enable a growing middle class, and stabilize local and regional society.
Building with bricks made from a plastic waste mixture is:
- Tested. Up to 20% of clay or cement can be easily replaced with scrap plastic without sacrificing strength and durability.
- Stable. The bricks are 5-7 times more stable and pressure-resistant than conventional concrete bricks.
- Practiced. Works as easily as regular concrete.
- Flame retardant and insulating. It has properties similar to traditional concrete or clay bricks. However, if they burn, the plastics release highly toxic gases.
- Safe from microplastic abrasion.
- Water repellent. Absorbs less water than traditional clay or concrete bricks. Can also be used for underwater structures.
- Versatile. Can be used for partitions, exterior walls and non-structural masonry.
- Cheap. The production costs per unit of plastic bricks are significantly lower than those of traditional clay or even concrete bricks. Reason: fewer working hours, water consumption and fractures, shorter curing times.
Working with this technology can also be:
- Labor-intensive. Melting plastic waste requires its own technology. Most are patented, which limits their processing.
- Expensive. It takes a lot of time to experiment, expertise and expensive machines.
- Not necessarily sustainable. When the plastic melts, toxic gases can be produced that must be captured. It also requires temperatures of 120-150 degrees Celsius and therefore energy, the climate balance of which depends on the energy source used.
- Not sufficiently researched. There are no studies on the long-term performance or environmental impact.
- Downcycling. Unlike Ecobricks, the individual components of the brick mixtures cannot be salvaged and are then likely to be used only as rubble or not at all.
- Opaque. What plastic is used – whether it comes from the environment and is not recyclable, or could have been upcycled- is not always visible.
Caution should be exercised as to who pursues this method and with what intention. All companies position themselves as “social” or sustainable companies that want to create jobs and make a difference. Many such as Gjenge Makers (Kenya), Ramtsilo (South Africa) and Rhino Machines (India) are 100% local owned. But behind others like Green Antz Builders (Philippines) is the Nestlé group, who could use this method to improve its recycling numbers.
Building blocks from 100% plastic waste
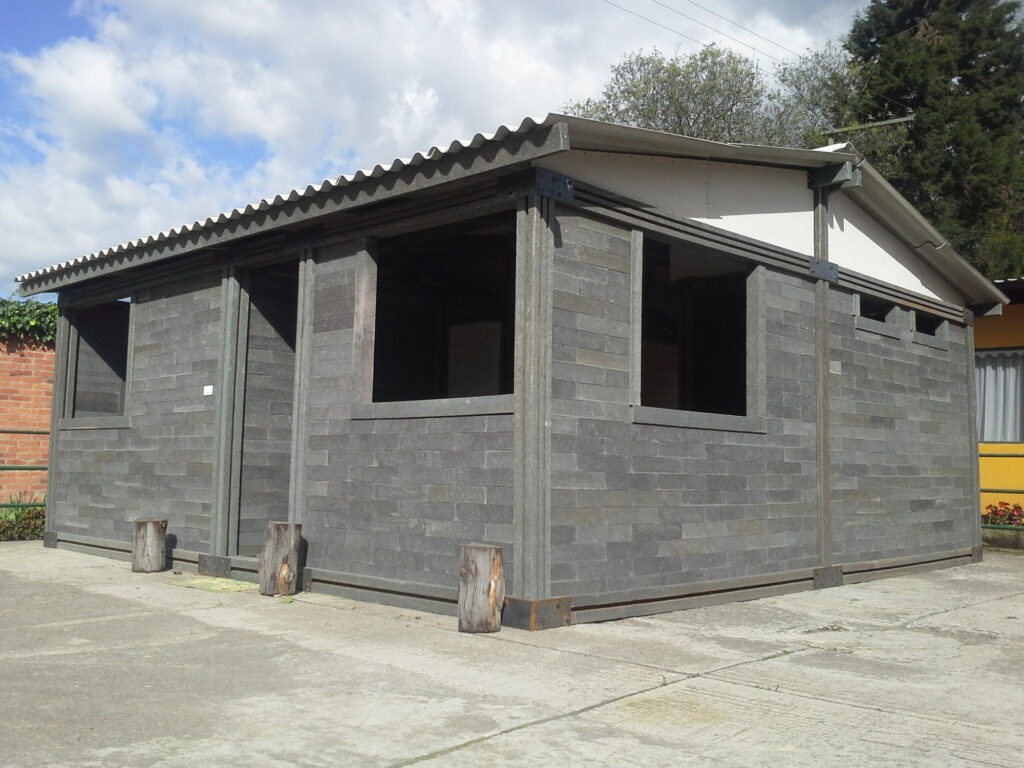
For about a decade, companies have also been trying their hand at the supreme discipline: manufacturing construction elements from 100% recycled plastic waste. Some have succeeded, others are still tinkering. In this technique, all pieces of plastic waste (preferably the non-recyclable ones) can be used – with the exception of Styrofoam. First, the plastic is collected and shredded. Then the shreds are melted into a paste and poured into a mold where they cool.
From the point of view of the method of production, most of the techniques are similar. The types of plastic that are used vary. So does their melting point and how much energy is needed to melt them down. What also differs greatly are the shapes and construction methods. This is well illustrated by the two most experienced companies that follow this construction method:
Conceptos Plásticos: The Colombian company has been in the market the longest. Since 2011, it has been producing elongated, gray plastic bricks that are built on top of each other with a click system like laminate – or like clamp bricks. At first glance, they don’t look like plastic bricks. The company works only with waste plastic that has been collected from nature or is non-recyclable. It uses its patented technology exclusively in developing countries and mostly for social purposes. Since 2019, it has been working with the United Nations Children’s Fund UNICEF to set up a brick factory in the West African country of Ivory Coast, where mainly classrooms are made.
By Fusion: Founded in 2017, the California-based company takes a slightly different approach. Through its patented recycling process, the waste plastic the company uses doesn’t even have to be cleaned up much. It is melted by steam and pressed into large blocks weighing 10 kilograms. No mortar or adhesives are needed for construction. The blocks are stacked on top of each other and interlocked with wire. Afterwards, they can be plastered or covered with wood.
The British non-profit organization Recycle Rebuild has taken yet another approach. In collaboration with the Dutch network Precious Plastics, it has developed a brick made of 100% waste plastic that resembles an oversized Lego brick. The project was entirely donation-based and the blueprint for making your own plastic bricks was made available to everyone on the Precious Plastic website. These can be used, for example, to build toilet blocks at festivals or bicycle sheds.
Read below to see the advantages and disadvantages we know from the research so far.
From the research, we know that building with Ecobricks is:
- Relatively simple. For all variants, no special construction knowledge is required, except for the design of the buildings.
- Waste free. Nothing is leftover during production,
- Water-resistant.
- Relatively fireproof. Houses made of plastic bricks are not more flammable than houses of wood frame construction. However, if they burn, the plastics release highly toxic gases.
- As strong or stronger than concrete structures.
- Recyclable. The building blocks can be reused.
- Energy-saving. The waste plastic is melted at temperatures of 90 to 130 degrees Celsius. This is much lower and requires less energy than the production of bricks from sand-lime (up to 200 degrees Celsius), clay (up to 1200 degrees Celsius) and cement clinker, a main component of cement needed for concrete production (up to 1450 degrees).
Building with 100% plastic bricks is also:
- Labor-intensive. Melting plastic waste into blocks requires its own technology. Most methods are patented, which limits their use.
- Expensive. It takes a lot of time to experiment, expertise, and space and expensive processing machinery. A starter kit from Precious Plastik with digital training and all the necessary machinery costs 9,300 euros.
- Not necessarily sustainable. Melting down the plastic can produce toxic gases that need to be captured.
- Not sufficiently researched. There is no publicly available research on the environmental impact of the production processes or application.
- Opaque. What plastic is being used – that which comes from the environment and is not recyclable, or that which could have been better upcycled? This is not always visible.
What plastic can do - and what it can't - as a building material
A jump back to the recycling village in Indonesia. According to Project Wings, the streets in Bukit Lawang became cleaner and the construction and deposit system helped some of the inhabitants who depend on tourism to get through the pandemic financially.
However, the organization cannot predict the exact impact of the project on the environment in Sumatra and its inhabitants, whether it will reduce waste mountains, save building materials or whether the construction method will find favor in the medium and long term and create more jobs. There would be too many factors involved. This is also the case for the other companies and for research, which is still needed.
The three methods of construction have very different advantages and disadvantages. Ecobricks are the cheapest and simplest method, which is especially suitable for regions with tropical climate. However, they replace clay bricks rather than concrete bricks. Their construction method also cannot be standardized, so it is not scalable. In contrast, the other two construction methods have already taken this step. Bricks made from a plastic mix or from 100% recycled scrap plastic follow sophisticated manufacturing processes and some have already been tested for security and fire safety measures. On the other hand, their production is expensive, and requires expertise and special equipment.
However, all three construction methods have one obstacle that is inhibiting the growth of the new industry: many countries do not yet have building codes specifically for the use of reused building materials.
Nevertheless, more and more people are liking the idea and getting into the business with their own local variants. That’s because they see the potential locally: littering, people living on the streets or in unstable, temporary homes, while the cost of building materials is becoming increasingly expensive due to sustainability concerns and resource scarcity.
For them, houses made of recycled plastic waste are not an ideal solution to the plastic flood, nor do they make the construction industry more sustainable. Houses made of recycled plastics can neither replace a functioning waste management system, nor do they address the plastic problem at its root: in overproduction and overconsumption. But they are also more than a stopgap solution. They are a real social solution that can be established right now with the knowledge needed to put affordable roofs over people’s heads, build places of education and sanitation, create jobs. In other words, to satisfy basic needs.
A Kenyan journalist researched for us on site how well building with recycled plastic works in practice and what impact a local project can have on the community. You’ll find his findings in the next article in our “Chain Reactions” series.
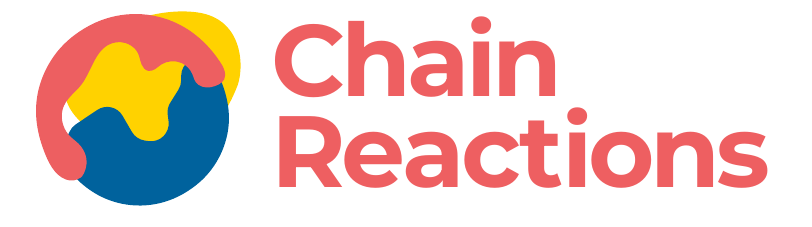
This project was funded by the European Journalism Centre, through the Solutions Journalism Accelerator. This fund is supported by the Bill & Melinda Gates Foundation.
Please consider a donation to support the work of our all-women newsroom. We create a space for journalists facing structural barriers, working towards a more equitable, inclusive world of journalism. Join our mission today!